Safety instructions symbols
Safety precautions
Safety instructions
- Before using the product, please read the user manual thoroughly and follow the safety rules.
- Keep this manual in a safe place for future reference.
- Do not modify, disassemble, or assemble the product arbitrarily.
- Observe the conditions of use specified on product's label or instruction.
- Operate, install, and disassemble product after confirming the safety of the surrounding conditions.
- For use in unspecified conditions or environments, we recommend that you thoroughly review safety measures and consult with us.
Qualifications of professional personnel
- We recommend handling by a person with sufficient knowledge and experience about the product.
- The person who determines the design or specifications of the system should determine whether the product is suitable for use.
Warranty and disclaimers
- For standard products, the warranty period is applied within 1 year from the date of use or within 18 months after delivery, whichever comes first.
- During the warranty period, if a failure or damage is clearly attributable to our company, we will provide a replacement/necessary replacement part, and we will not bear any additional loss. Warranty here means the warranty for our products, and any other damage caused by the failure of the product is excluded from the scope of the warranty.
Specifications
- Fluid
- Working fluid: compressed air
- Operation: class 1 turbine oil ISO VG32, VG46
- Fluid Temp.: 5~60℃
- Lubricant : none-lubricant (However, when lubricating,use turbine oil ISO VG32 or equivalent.)
- Operating pressure: 0~7kgf/㎠ (0~0.7MPa)
- Operating method: Direct pressure type (DI), Pre-pressure type (PP)
- Pneumatic tube bore size: Ø100, Ø150, Ø180, Ø300
- Standard stroke: 120, 200, 300, 200mm
- Boosting ratio: 8 to 36 times
- For detailed specifications, please refer to the individual catalog (KBP).
Product configuration
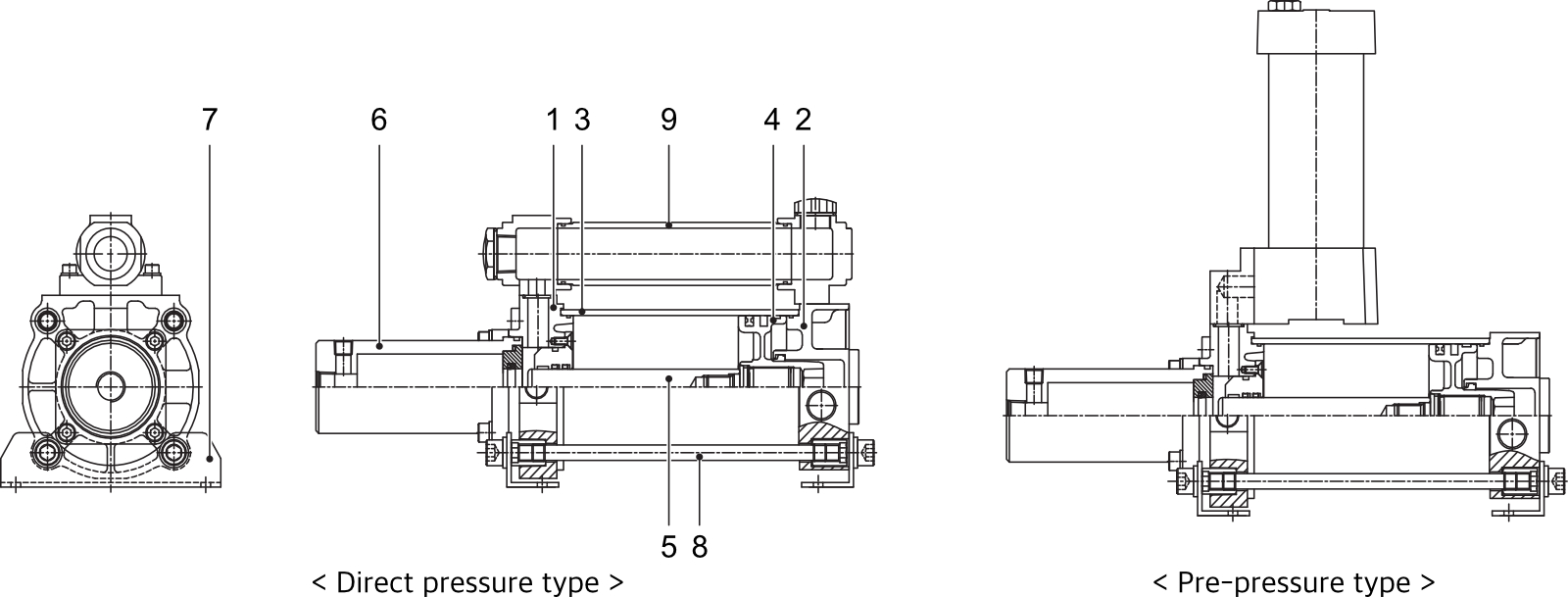
Assembly and operating
Precautions before installation
<div class="ico_danger">The installation or removal of a pressurized product may have risks of injuries and damages.</div>
<div class="ico_danger">Before performing removal work, MAKE SURE that the pressure in the product and the piping is released completely.</div>
<div class="ico_warn">For the maintenance and safe operation of the product, secure some space around the product.</div>
- Check if the model name and the specification of the product are in line with the installation environment.
- Protect the tube from damage when moving or handling the booster cylinder.
- Do not install the product at a place with high humidity or temperature. This may result in compromised performance or malfunction of the product.
- A booster cylinder must be installed higher than the hydraulic cylinder and the piping for venting the air in case there is reflux of the hydraulic oil.
- Make sure there is no external magnetism near the booster cylinder. External magnetism may cause malfunction of the Auto Switch.
- An increase of only 0.1 kgf/㎠ in the supply-side pressure will result in multiplied output based on the factor of pressurization. Caution is required.
- If you require high speed, increase the size of the piping. In this case, you need to install a rapid exhaust valve.
- For easier regulation of pressure and supply of clean air, install a filter and a regulator before the air valve.
- The exhaust rate of the booster cylinder must be the same as the capacity of the cylinder that can generate power.
- After installing the booster cylinder, be sure to go through the test run stage to check for any leak and confirm proper functioning before putting the equipment into operation.
Installation
- Use the provided bracket to fix the booster cylinder firmly.
- Make sure that the cylinder axis remains parallel. Likewise, prepare a measure to prevent vibration.
- Connect the pneumatic hose and the hydraulic hose to the input port and the output port, respectively.
- Adjust the route of the piping to ensure that the hose neither gets folded nor sags excessively.
- When using a solenoid valve, follow the safety rules for electrical installation works. The connections must be made while power is cut off.
- Before engaging the pneumatic power supply, make sure all components are installed properly.
Pneumatic piping
<div class="ico_warn">Connect the pneumatic pipes only after completing the attachment of the booster cylinder.</div>
- Before connecting the pipes, perform sufficient flushing or washing of the pipes, etc., to remove any foreign objects inside the pipes.
If the piping or fitting is connected using screws, take caution to avoid any breakage of the piping screws or entry of any foreign objects inside the equipment.
This may cause malfunction of the product. - Connect the screw of the piping or fitting to the pneumatic port. Follow the torque ratings when making the connections.
- Perfectly seal the pneumatic port, and then connect the pneumatic tube.
- When operating the air hydro converter, there may be a slight sliding leak. On the exhaust side of the solenoid valve, be sure to install an exhaust cleaner.
Hydraulic piping
- Before connecting the pipes, perform sufficient flushing or washing of the pipes, etc., to remove any foreign objects inside the pipes.
If the piping or fitting is connected using screws, take caution to avoid any breakage of the piping screws or entry of any foreign objects inside the equipment. This may cause malfunction of the product. - Connect the screw of the piping or the fitting to the hydraulic port. Follow the torque ratings when making the connections.
- Perfectly seal the hydraulic port, and then connect the hydraulic hose.
- There may be bubbles in the hydraulic piping during operation due to cavitation. Therefore, make this as short as possible.
Oil injection
When injecting oil, use Type 1 ISO VG32 or VG46.
Direct pressure method
- Remove the oil injection plug of the oil tank located on top of the booster cylinder.
- Replenish oil up to or beyond the red markings on the level gauge located on the side of the oil tank. Then, activate the actuator.
- Operate the actuator repeatedly to fill up the actuator and the hydraulic pipes with oil.
- Supply oil so that, after the return cycle of the actuator, the level of the oil reaches or goes beyond the red marking of the level gauge of the oil tank.
- Connect the dismounted oiling plug to the oil inlet of the oil tank of the booster cylinder.
Preload method
- Remove the oil injection plug located on the topside of the hydro-converter. (Take caution not to use the packing while dismounting.)
- Supply oil up to the red line on the HIGH side of the level gauge of the hydro-converter. Then, activate the actuator.
- Operate the actuator repeatedly to fill up the actuator and the hydraulic pipes with oil.
- Supply oil so that, after the return cycle of the actuator, the level of the oil comes between the High and Low levels of the level gauge of the air-hydro-converter.
- Connect the dismounted oiling plug to the oil inlet of the oil tank of the air-hydro-converter.
- When replenishing the oil, supply oil so that the oil level after a return cycle of the actuator comes between the High and Low positions while the oil level at the level gauge of the air-hydro-converter comes below the red line of the LOW position.
- Before activating the actuator, be sure to vent out the air.
Dismantling
<div class="ico_warn">Before performing removal work, MAKE SURE that the pressure in the product and the piping is released completely.</div>
Dismantling of the pneumatic piping
- Vent out the air from the product and the entire system.
- Press and release the locking mechanism from the piping or fittings. Then, pull out and remove the hose.
- Release the fitting from the connecting flange. Then, rotate the fitting and remove it.
Dismantling of the hydraulic piping
- Vent out the air from the product and the entire system.
- Release and remove the hydraulic hose connected to the fitting.
- Loosen and disconnect the screw connector of the piping or fitting from the hydraulic port.
Examples of use
A booster cylinder can be configured in a direct pressure configuration or a preload configuration depending on how you wish to use the product.
Direct pressure method
- All hydraulic cylinder cycles are pressurized segments.
- The capacity of the hydraulic cylinder and hydraulic pipes must not exceed the exhaust volume of the booster cylinder.
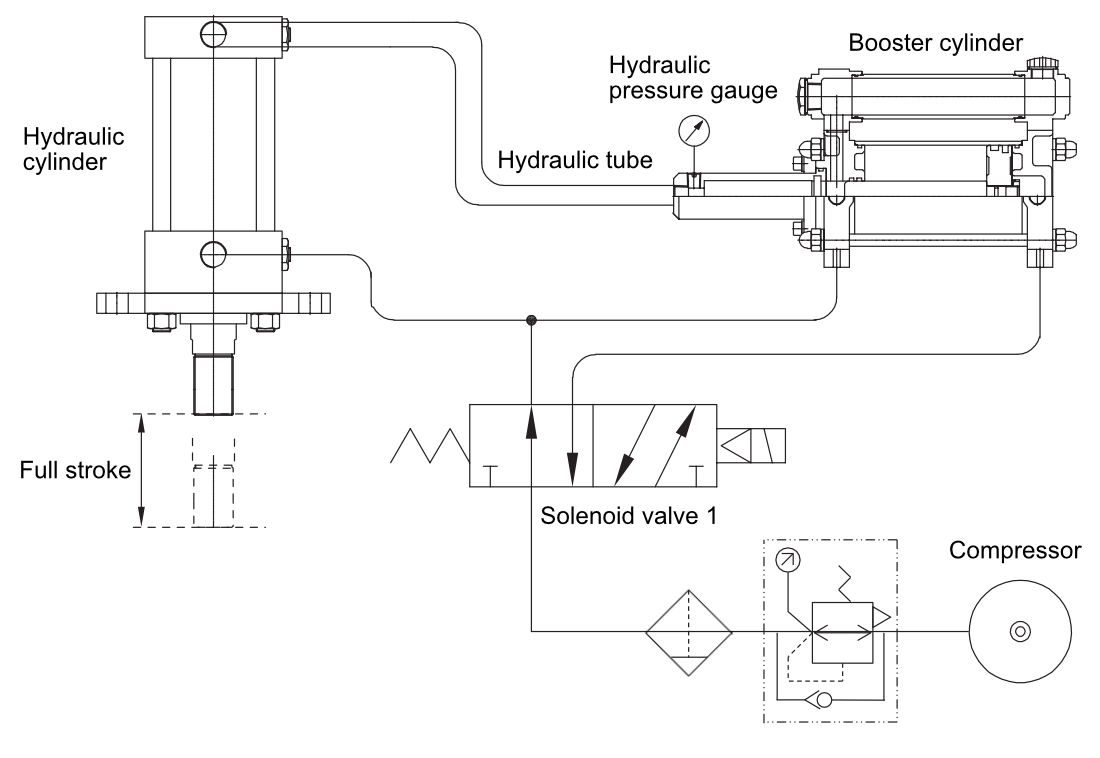
Pre-pressure method
- This method is used when the cycles of the hydraulic cylinder are long or the flow rate is high.
- Move to the pressurized section through the air. Then, the rest of the cycles are pressurized using the exhaust volume.
- Transfer cycle
The air moves the cylinder rod to a certain position using the same level of hydraulic pressure (through the converter) initially through Solenoid valve 1.
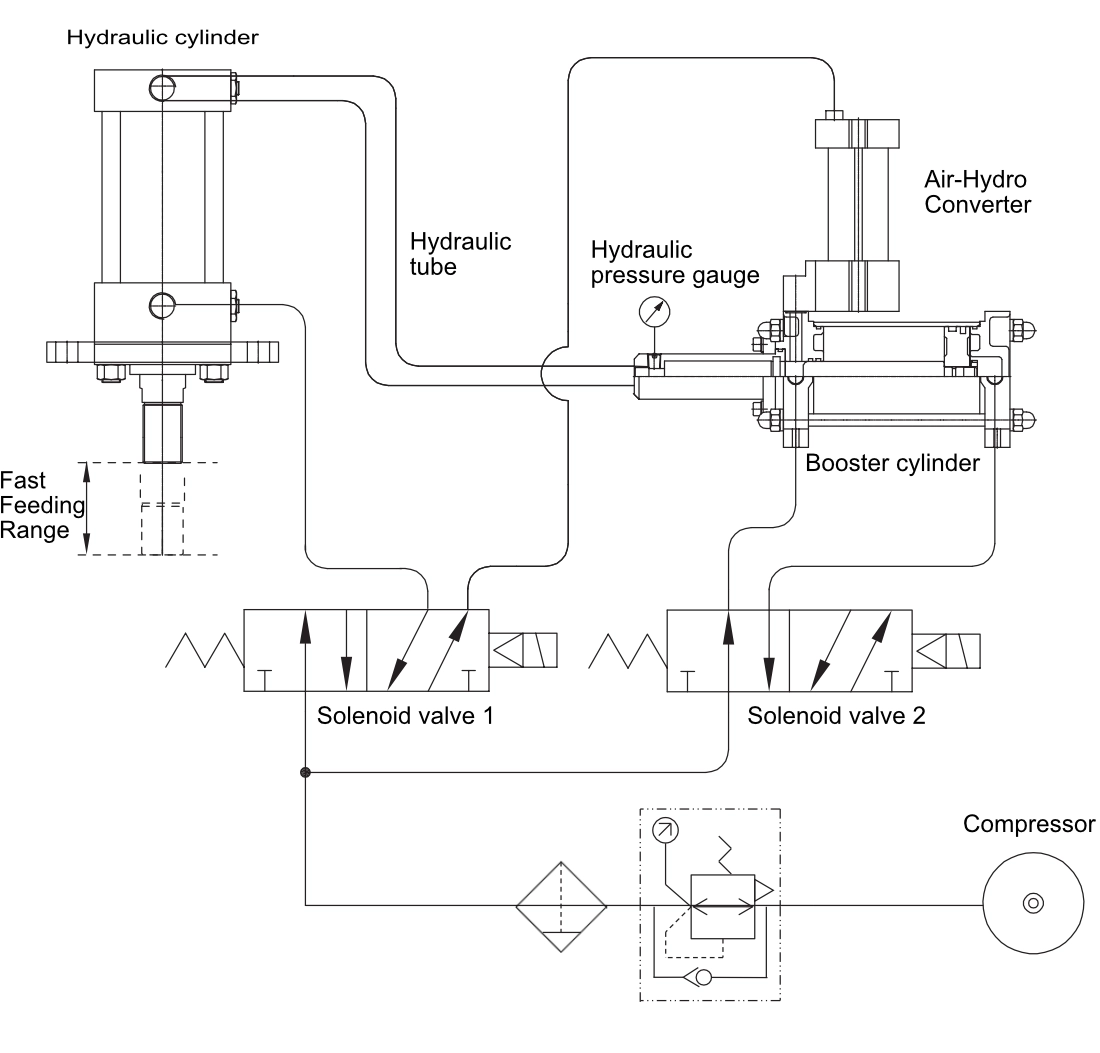
- Pressing cycle
Solenoid Valve 2 pressurizes the booster piston to create high hydraulic pressure to perform the job.
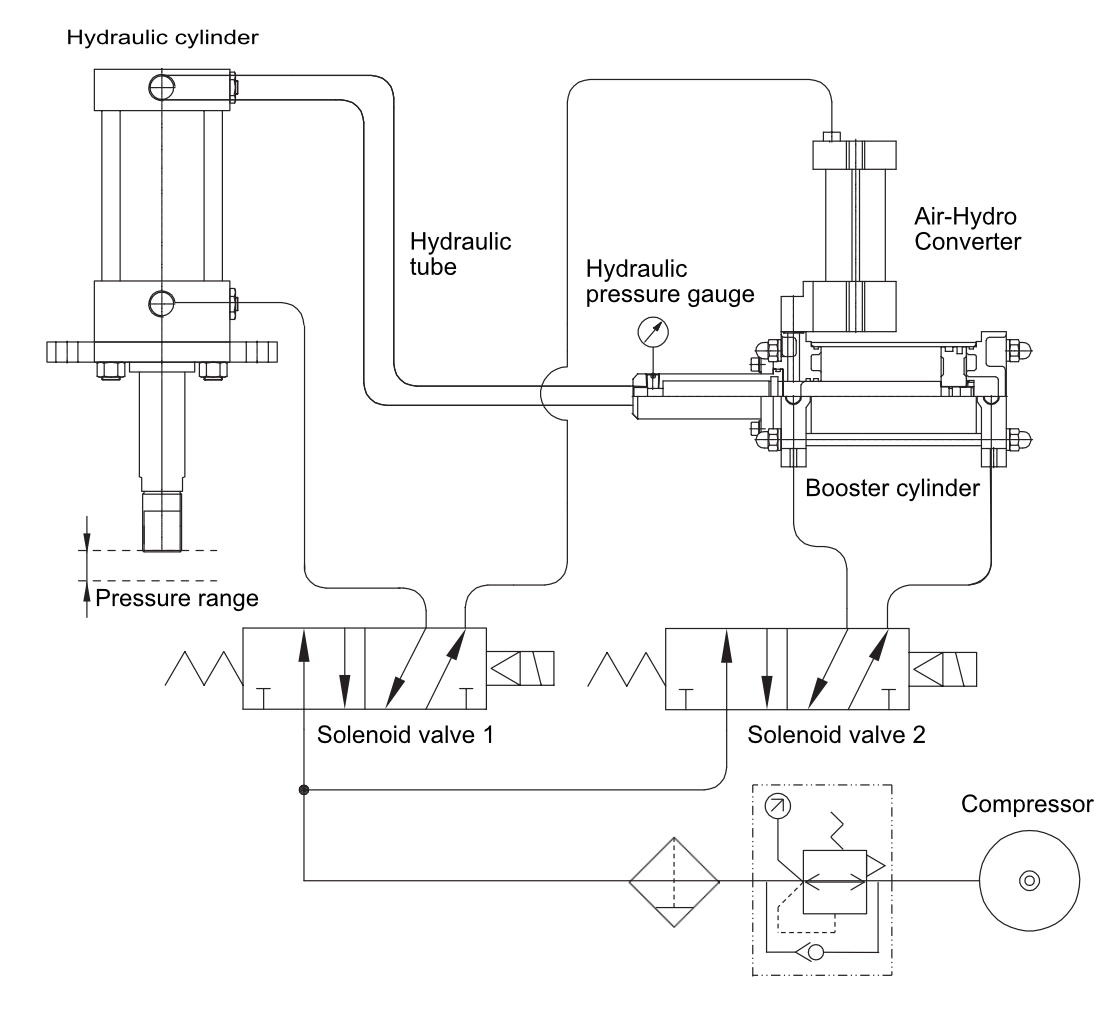
- Return cycle
Solenoid valves 1 and 2 return the booster piston and the cylinder piston to the home positions.
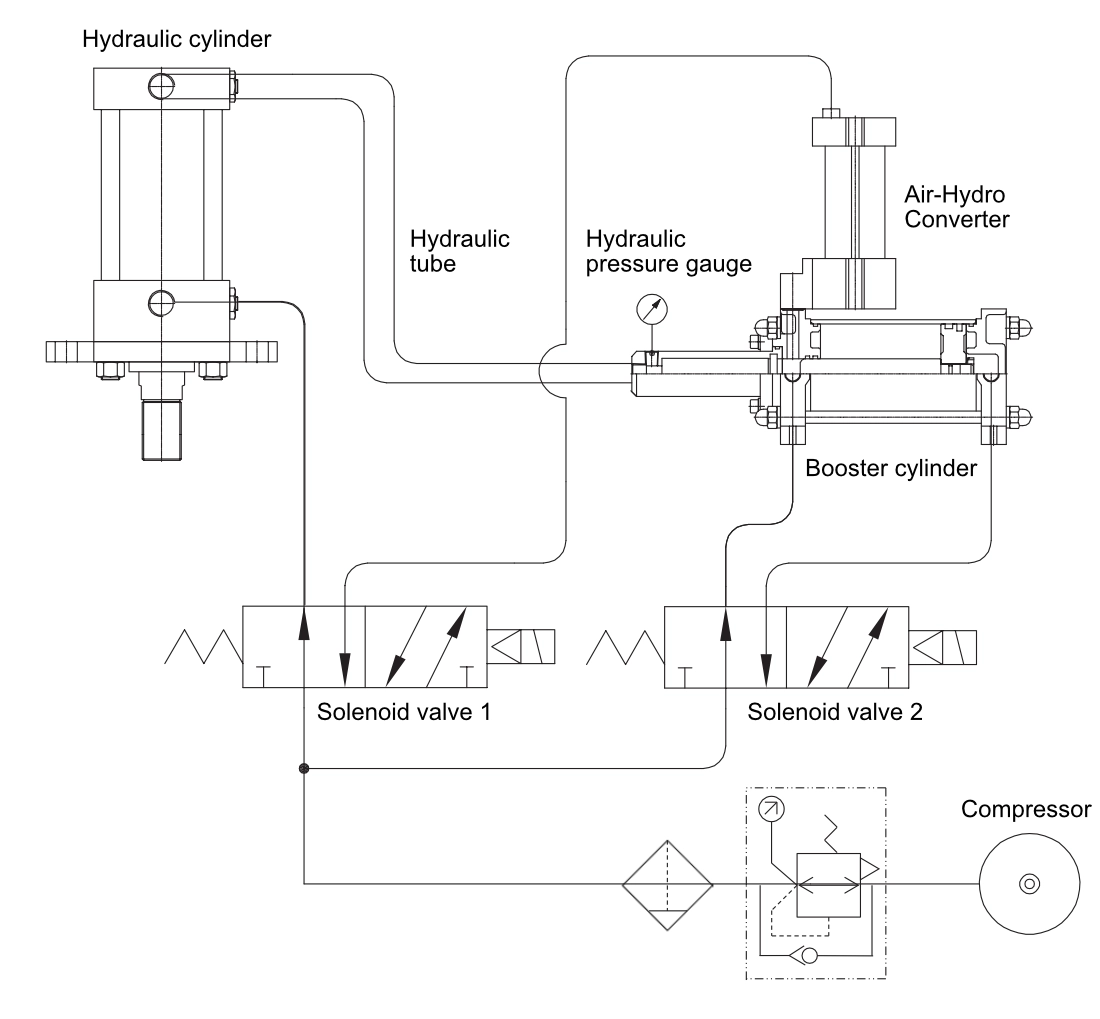
Maintenance
Air supply
- Use clean air only. The filtering level of the air filter must not exceed 5 ㎛.
- Any chemicals, organic solvents, synthetic oil, or corrosive gas in the air may cause damage or malfunction of the components.
- Air with high level of moisture or foreign objects may cause malfunction. Install an air-dryer or an after-cooler at the inlet of the product.
Operation environment
- Protect the product from direct sunlight or radiation heat.
- Inspect the attachment, end caps, tie-rods, loosening of the bolts, and connection with external devices on a regular basis.
- Regularly check for damage or contamination on the exterior of the booster cylinder and pneumatic hoses.
- Regularly check if the output pressure is within the specification.
- Check if there is any air leak at the pneumatic connections or from the inside of the cylinder.
- Wipe the exterior of the cylinder clean and keep off dust or foreign contaminants.
- Permitted cleaning agents: soap water (up to 60℃)
Neutral detergents (free of aromatic compounds)
Failures and measures
Influx of foreign contaminants.
- Remove the foreign contaminants inside the high-pressure tube of the booster cylinder and hydraulic pipes.
Then, replace the packing.
In case there is water in the supplied air.
- Remove the moisture inside the booster cylinder and air pipes and takemeasures to keep the air clean.
If there are any foreigncontaminants inside.
- Remove foreign matter from inside the booster cylinder and air pipe.
- Replace the packing seal.
Insufficient piston speed or supply pressure.
- Adjust the supply pressure and check the minimum operating speed according to the specifications.
For additional information, please visit our web site or contact us.